El revestimiento de plástico es un proceso de revestimiento que se ha utilizado ampliamente en la industria electrónica, la investigación de defensa, los electrodomésticos y las necesidades diarias.La aplicación del proceso de revestimiento de plástico ha ahorrado una gran cantidad de materiales metálicos, su proceso de procesamiento es más simple y su propio peso es más liviano en comparación con los materiales metálicos, por lo que el equipo producido mediante el proceso de revestimiento de plástico también se reduce en peso, lo que también hace que el Aspecto de piezas plásticas con mayor resistencia mecánica, más bellas y duraderas.
La calidad del revestimiento de plástico es muy importante.Hay muchos factores que afectan la calidad del revestimiento de plástico, incluido el proceso de revestimiento, la operación y el proceso del plástico, que pueden tener un impacto significativo en la calidad del revestimiento de plástico.
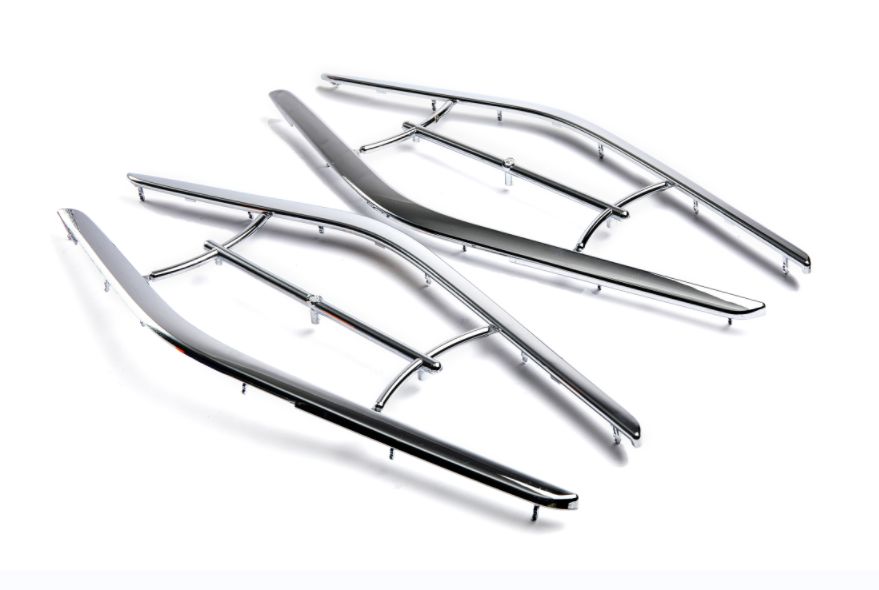
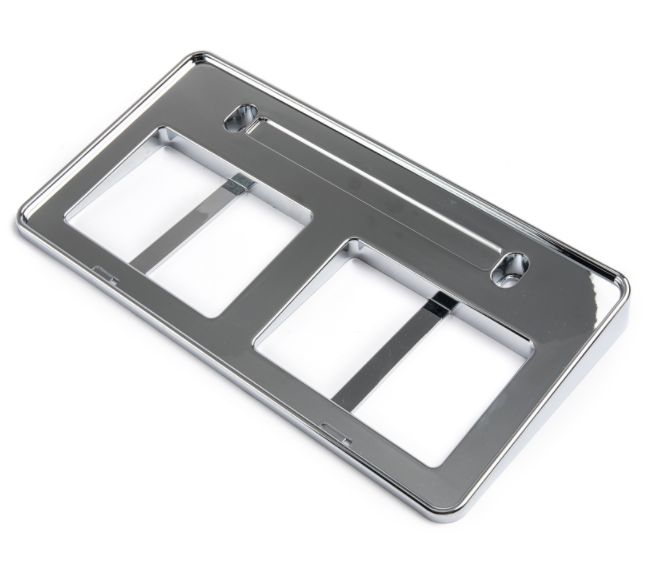
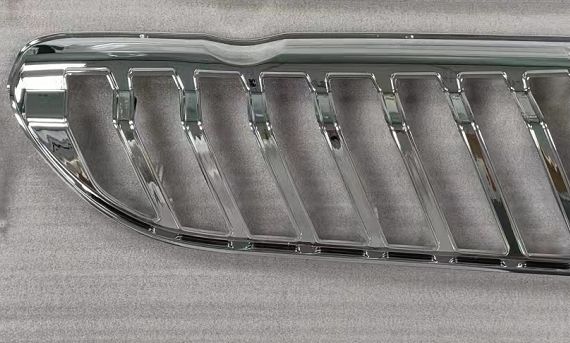
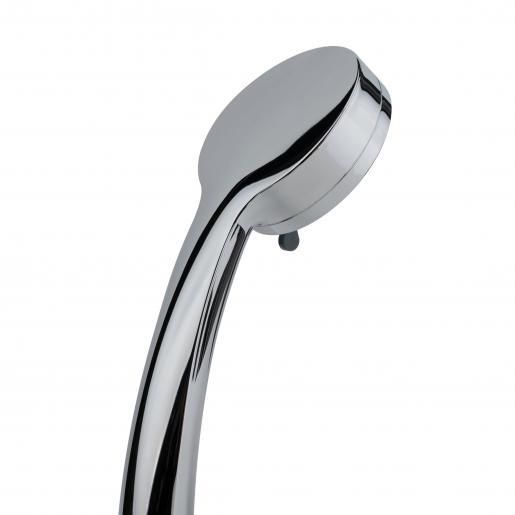
1. Selección de materia prima
Hay muchos tipos diferentes de plásticos en el mercado, pero no todos se pueden recubrir, ya que cada plástico tiene sus propias propiedades, y al recubrir es necesario considerar la unión entre el plástico y la capa metálica y la similitud entre las propiedades físicas de el plástico y el revestimiento metálico.Los plásticos disponibles actualmente para el revestimiento son ABS y PP.
2.Forma de las piezas
A).El espesor de la pieza de plástico debe ser uniforme para evitar irregularidades que provoquen una contracción de la pieza de plástico; cuando se completa el revestimiento, su brillo metálico provoca una contracción más evidente al mismo tiempo.
Y la pared de la pieza de plástico no debe ser demasiado delgada, de lo contrario se deformará fácilmente durante el revestimiento y la unión del revestimiento será deficiente, mientras que la rigidez se reducirá y el revestimiento se caerá fácilmente durante el uso.
B).Evite los agujeros ciegos; de lo contrario, la solución de tratamiento residual en el solenoide ciego no se limpiará fácilmente y provocará contaminación en el siguiente proceso, afectando así la calidad del revestimiento.
C).Si el revestimiento tiene bordes afilados, será más difícil hacerlo, ya que los bordes afilados no solo generarán energía, sino que también harán que el revestimiento se abulte en las esquinas, por lo que debe intentar elegir una transición de esquina redondeada con un radio de al menos 0,3 mm.
Al recubrir piezas planas de plástico, intente cambiar el plano a una forma ligeramente redondeada o haga una superficie mate para revestir, porque la forma plana tendrá un revestimiento desigual con un centro delgado y un borde grueso al revestir.Además, para aumentar la uniformidad del brillo del revestimiento, intente diseñar piezas de plástico con una gran superficie de revestimiento para que tengan una forma ligeramente parabólica.
D).Minimice los huecos y protuberancias en las piezas de plástico, ya que los huecos profundos tienden a revelar el plástico al enchapar y las protuberancias tienden a quemarse.La profundidad de la ranura no debe exceder 1/3 del ancho de la ranura y el fondo debe estar redondeado.Cuando hay reja, el ancho del hueco debe ser igual al ancho de la viga y menor a la mitad del espesor.
MI).Se deben diseñar suficientes posiciones de montaje en la parte chapada y la superficie de contacto con la herramienta para colgar debe ser de 2 a 3 veces mayor que la de la parte metálica.
F).Las piezas de plástico deben revestirse en el molde y desmoldarse después del revestimiento, por lo que el diseño debe garantizar que las piezas de plástico sean fáciles de desmoldar para no manipular la superficie de las piezas revestidas ni afectar la unión del revestimiento al forzarlo durante el desmolde. .
GRAMO).Cuando se requiere moleteado, la dirección del moleteado debe ser la misma que la dirección del desmolde y en línea recta.La distancia entre las franjas moleteadas y las franjas debe ser lo más grande posible.
H).Para piezas de plástico que requieren incrustaciones, evite el uso de incrustaciones de metal tanto como sea posible debido a la naturaleza corrosiva del tratamiento antes del revestimiento.
I).Si la superficie de la pieza de plástico es demasiado lisa, no favorece la formación de la capa de revestimiento, por lo que la superficie de la pieza de plástico secundaria debe tener una cierta rugosidad superficial.
3.Diseño y fabricación de moldes.
A).El material del molde no debe ser una aleación de bronce y berilio, sino acero fundido al vacío de alta calidad.La superficie de la cavidad debe pulirse hasta obtener un brillo de espejo a lo largo de la dirección del molde, con un desnivel de menos de 0,21 μm, y la superficie debe revestirse preferiblemente con cromo duro.
B).La superficie de la pieza de plástico refleja la superficie de la cavidad del molde, por lo que la cavidad del molde de la pieza de plástico galvanizada debe estar muy limpia y la rugosidad de la superficie de la cavidad del molde debe ser 12 grados mayor que la rugosidad de la superficie de la parte.
C).La superficie de separación, la línea de fusión y la línea de incrustación del núcleo no deben diseñarse en la superficie revestida.
D).La puerta debe diseñarse en la parte más gruesa de la pieza.Para evitar que la masa fundida se enfríe demasiado rápido al llenar la cavidad, la compuerta debe ser lo más grande posible (aproximadamente un 10% más grande que el molde de inyección normal), preferiblemente con una sección transversal redonda de la compuerta y el bebedero, y la longitud de el bebedero debe ser más corto.
MI).Se deben proporcionar orificios de escape para evitar defectos como filamentos de aire y burbujas en la superficie de la pieza.
F).El mecanismo eyector debe seleccionarse de tal manera que garantice una liberación suave de la pieza del molde.
4.Condición del proceso de moldeo por inyección para piezas de plástico.
Debido a las características del proceso de moldeo por inyección, las tensiones internas son inevitables, pero un control adecuado de las condiciones del proceso reducirá las tensiones internas al mínimo y garantizará el uso normal de las piezas.
Los siguientes factores influyen en la tensión interna de las condiciones del proceso.
A).Secado de materia prima
En el proceso de moldeo por inyección, si la materia prima utilizada para recubrir las piezas no está lo suficientemente seca, la superficie de las piezas producirá fácilmente filamentos de aire y burbujas, lo que afectará la apariencia del recubrimiento y la fuerza de unión.
B).Temperatura del molde
La temperatura del molde tiene una influencia directa sobre la fuerza de unión de la capa de revestimiento.Cuando la temperatura del molde es alta, la resina fluirá bien y la tensión residual de la pieza será pequeña, lo que favorece la mejora de la fuerza de unión de la capa de revestimiento.Si la temperatura del molde es demasiado baja, es fácil formar dos capas intermedias, de modo que el metal no se deposite durante el revestimiento.
C).Temperatura de procesamiento
Si la temperatura de procesamiento es demasiado alta, provocará una contracción desigual, aumentando así la tensión de temperatura del volumen, y la presión de sellado también aumentará, lo que requerirá un tiempo de enfriamiento prolongado para un desmolde sin problemas.Por lo tanto, la temperatura de procesamiento no debe ser ni demasiado baja ni demasiado alta.La temperatura de la boquilla debe ser inferior a la temperatura máxima del cañón para evitar que el plástico fluya.Para evitar que el material frío entre en la cavidad del molde, a fin de evitar la producción de grumos, piedras y otros defectos y provocar la combinación de un revestimiento deficiente.
D).Velocidad, tiempo y presión de inyección.
Si estos tres no se dominan bien, provocará un aumento de la tensión residual, por lo que la velocidad de inyección debe ser lenta, el tiempo de inyección debe ser lo más corto posible y la presión de inyección no debe ser demasiado alta, lo que reducirá efectivamente los residuos. estrés.
MI).Tiempo de enfriamiento
El tiempo de enfriamiento debe controlarse de modo que la tensión residual en la cavidad del molde se reduzca a un nivel muy bajo o cercano a cero antes de abrir el molde.Si el tiempo de enfriamiento es demasiado corto, el desmoldeo forzado provocará grandes tensiones internas en la pieza.Sin embargo, el tiempo de enfriamiento no debe ser demasiado largo; de lo contrario, no solo la eficiencia de producción será baja, sino que también la contracción por enfriamiento provocará tensiones de tracción entre las capas interior y exterior de la pieza.Ambos extremos reducirán la unión del revestimiento sobre la pieza de plástico.
F).La influencia de los agentes de liberación.
Es mejor no utilizar agentes desmoldantes para piezas de plástico revestidas.No se permiten agentes desmoldantes a base de aceite, ya que pueden causar cambios químicos en la capa superficial de la pieza de plástico y alterar sus propiedades químicas, lo que resulta en una mala unión del revestimiento.
En los casos en los que se deba utilizar un desmoldante, sólo se debe utilizar talco o agua con jabón para desmoldar.
Debido a los diferentes factores que influyen en el proceso de revestimiento, las piezas de plástico están sometidas a diferentes grados de tensión interna, lo que conduce a una reducción de la unión del revestimiento y requiere un tratamiento posterior eficaz para aumentar la unión del revestimiento.
Actualmente, el uso de tratamientos térmicos y tratamientos con agentes de acabado de superficies tiene un muy buen efecto en la eliminación de tensiones internas en piezas de plástico.
Además, las piezas chapadas deben embalarse e inspeccionarse con sumo cuidado y se debe realizar un embalaje especial para evitar dañar la apariencia de las piezas chapadas.
Xiamen Ruicheng Industrial Design Co., Ltd tiene una amplia experiencia en revestimiento de plástico. ¡No dude en comunicarse con nosotros si tiene alguna necesidad!
Hora de publicación: 22 de febrero de 2023